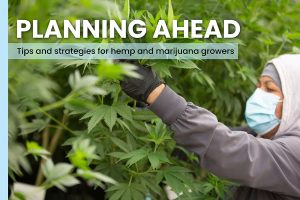
(This is the 11th installment in a series focused on cultivation planning for hemp and marijuana growers. The previous installment is available here.)
For a cannabis cultivator, fertilizer and irrigation can be some of the steepest costs after labor. But the two steps are arguably the most important parts of any grow operation.
Enter the term “fertigation,” which combines the two systems into one word.
To that end, many cannabis growers often use automated fertigation systems that control the flow of both nutrients and water to their plants.
Beyond automation, there are several ways for cultivators to cut down on fertigation production costs and maximize efficiencies, including:
- Mixing fertilizer ingredients in-house.
- Keeping the system clean and operational.
- Recirculating and testing the water.
DIY nutrients
Premixed plant nutrients can be convenient. Just dump and go.
But taking the time to formulate in-house recipes that can be tweaked depending on the plant cycle and changes to the municipal water, for example, can ultimately yield financial dividends.
Nick Drury, senior vice president of cultivation for Denver-based cannabis cultivator and retailer Lightshade, uses a combination of raw salts for his custom fertilizer formulations.
The greenhouse recipe has several parts, including magnesium sulfate, calcium nitrate, potassium nitrate and monopotassium phosphate. His indoor-grow recipe has fewer parts but uses the same raw salts – just combined.
Drury said the savings of in-house-formulated versus premixed nutrients are “huge.” He estimates the company saves $300,000-$500,000 a year by not buying off the shelf.
The other benefit: Growers know exactly what they’re putting into their plants.
That’s a selling point for William Brinkerhoff Jr., CEO of Lost Coast, a cannabis company with a cultivation facility in Rocky Ford, Colorado.
“We make sure we’re sticking to giving our consumers good medicine,” he said.
His cultivation team runs a low-tech drip-line system, and instead of using an automated machine to measure the water and nutrients, workers walk the garden and feel how much moisture the plants might need.
A higher-quality flower yield is another benefit of mixing nutrients, Brinkerhoff said.
“If you can do it right, you do it for the same cost or less,” he added. “There is a labor cost involved, but we think it makes sense from a business perspective.”
At Molecular Farms, a research and development cannabis production facility in Salinas, California, Operations Manager Steven Haba uses all organic nutrients, which are regulated by an automated controller that connects to his drip irrigation-based system.
Haba uses a different nutrient formulation depending on the crop cycle, with a balance of micro and macro nutrients.
“Nutrients can be tremendously expensive, so knowing what’s going on with your plants at different parts of the cycle is crucial,” he said.
Haba estimates he cuts his costs for fertilizer by 60%-70% by mixing his own.
“Beyond it being cost-effective, it gives awareness to all employees of what we’re putting into the plants,” he said.
Keep it clean
For Ed Dow, CEO of Solar Therapeutics, a cannabis cultivation facility with retail dispensaries based in Somerset, Massachusetts, successful fertigation comes down to cleanliness.
“If you don’t keep your system clean, you could have a failed crop,” Dow said.
The fertigation lines could generate excessive microbials, including yeast and mold.
His team cleans the lines and trays daily – “anywhere that comes into contact with the water and nutrients.”
Dow said his company is always building on its standard operating procedures, whether that’s daily, weekly, monthly or quarterly.
He’s found liquid ozone a useful solvent in mitigating microorganisms.
Recirculate, test, repeat
Solar Therapeutics recirculates its fertigation water back into holding tanks, then flushes it with ozone and reuses it.
The company sends the water to a third-party lab every few months. Dow said the city water can have different microorganisms or the pH can change and the fertigation mixture needs to be adjusted accordingly.
Haba’s operation in Salinas uses well water, which can vary slightly in calcium carbonate and pH, and he adjusts his nutrients accordingly.
His team checks the moisture level of the soil by looking for how much water is leaching out of the bottom of the pots then weighing them.
He tests the plants using sap analysis, which gives him an opportunity to look at what nutrients are in the leaves at different parts of the canopy. He uses that method twice a month, to see how much or how little the nutrients need to be adjusted.
At Lost Coast, the team tests the soil and also conducts sap tests along with testing its water. Once Brinkerhoff discovered the company’s water lacked ionization, he mixed his nutrients to account for that.
Drury of Lightshade relies on soil sensors to determine what the plants need and at what strength to irrigate.
He’s a big proponent of using analytics and data in his grow room. He tests for soil moisture as well as the electric conductivity of the soil, which is largely dependent on the amount of salt.
“Use data to make highly replicable, nonsubjective fertigation decisions,” Drury advised.
Bart Schaneman can be reached at [email protected].